- 关键词:
- 摘要:机器视觉是指使用工业相机对产品进行拍照,检测,输出结果,机构利用结果进行剔除等动作。根据机械视觉的工序,就会涉及到产品的定位,光源,拍照,检测工具,输出I/O等。下面我们会通过案例对大家进行讲解。
机器视觉:我对机器视觉的理解是使用工业相机对产品进行拍照,检测,输出结果,机构利用结果进行剔除等动作。根据机械视觉的工序,就会涉及到产品的定位,光源,拍照,检测工具,输出I/O等。
我们最近有个案例就是视觉系统的一个缩影。先介绍一下,该案例是对洗发液瓶子的检测,有三种大小不一的规格,检测内容包括瓶盖有无,是否盖好,以及瓶子的正反面的批号检测。
1.定位
对象或特征的精确定位是一个检测系统或由视觉引导的运动系统的重要功能。瓶子在运行中可定会出现位置的不稳定,而且有三种大小不一的产品规格,如何确保每次的位置一致呢?该案例,我们克服定位不稳定的方式主要是机构保证和视觉定位。
1)机构传感器
机构保证,当然是靠传感器来确保,由于有三种大小不一的产品规格,怎么样才能让客户更换产品更方便?我们就根据三种规格的高度,标签的位置设置了一款传感器的支架,如下图,三个高度分别是三个档位,生产不同的产品,只要使用相对应的档位传感器即可,一秒即可!
2)视觉定位
使用Conmeas软件,对产品进行更为精确的定位,conmeas软件是我们自己开发的软件,视觉的定位就是使用模板,在搜索的局域内先寻找模板,进行初定位,从而使检测框跟随产品一起移动,避免了产品字符批号太小,无法找寻的问题。
2.光源与照明
众所周知,适当的灯光和照明对视觉应用的成功至关重要。有时,尽管选择了最合适的灯光和照明,但是,如果被监测 的对象或特征稍微变动一下,就要求相应改变灯光和照明亮度,故一切光源均需要良好的定位作为基础的根据检测不同的项目自然需要选用不同的光源,该案例主要检测瓶盖,与瓶身的批号。
瓶盖的检测:1)有无瓶盖检测 2)瓶盖是否盖好
根据这两项内容,很容易的想到使用灰度来检测,自然使用背光源。
平身正反面的批号检测:需要检测批号,使用条形灯。如果你想只用普通的条形灯,那就错了。
1)由于产品运动快,安装环境昏暗;
2)产品的大小不一,正反面的批号的高度也不一,产品运动中检测,环境昏暗自然需要亮度较大的光源,同时产品的大小不一,也涉及到相机景深的问题,外部光源强大,那光圈就可以打小点,景深会大,另外产品的正反面批号的高度不一样,自然也要考虑到光源的安装位置问题,根据这些考虑,该案例了频闪条形灯。产品经过时,光源闪亮,能瞬间产生高亮光。另外使用频闪光源,还有其它好处,省电,减少光污染。
3.视觉检测
针对检测内容,一共用了三个相机,相机一检测正面批号,相机二检测反面批号,相机三检测瓶盖情况,下面我们介绍一下各个相机的检测情况
1)相机一,相机二检测批号方法是一样的
a, 图象预处理
由于瓶子上的批号在运动中,亮度和对象表面或材料不同是会有变化的,所以图像预处理是非常的重要。图象预处理算法能把批号的特征点放大,以使视觉工具能更好的检测它们,去除其它杂点以至视觉工具能更准确稳定的检测。
b, OCV检测
使用Conmeas软件使用OCV的检测方式,使用该检测方式最大的特点是操作方便,按照我们平常对OCV的理解,OCV需要训练很多字符,这个是件很麻烦的事,一般是需要建立一个字符库的,为了方便操作,我们简化了很多繁琐的步骤,只需要点击一个训练的按钮,添加即可。
2)相机三检测瓶盖的有无,瓶盖是否拧好
检测瓶盖的有无,只需要在瓶盖的位置检测灰度即可,没有瓶盖的时候,灰度为255,有瓶盖的时候灰度为170左右,这样就足以判别,另外有瓶盖,但瓶盖并没有拧好与又该证明去判断呢?其实原理也是一样的,就如下面的图片一样,拧不好或者拧过了的瓶盖也会露出一些空白的地方,因为有了良好的定位工具的保证,检测框会随着瓶子精确移动,故值需要把检测框放置在瓶盖的边缘,检测灰度即可。
3)输出I/O
产品的输出信号相对来说比较简单,把产品照片处理后的NG信号发给PLC
应用循环时间:
现场产品运行的时间为5pcs/s, Conmeas软件简化了拍照时间和拍照后图片的处理时间,才能适应快速生产的要求
产品长时间测试:
现场产品经过一个月的测试,能达到误检测为1‰,漏检为零。
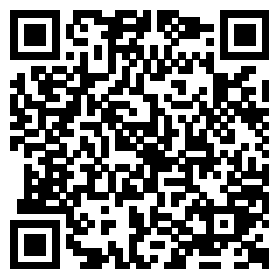
手机扫描二维码分享本页
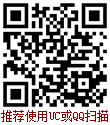
工控资讯APP 安卓版下载
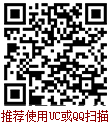
工控资讯APP IOS版下载
评价: | 一般 | ||