采用粉体样品的流化曲线去分析样品制备的可重复性
3D打印技术是当下最热门的话题,涉及到方方面面,从打印玩偶、武器、服装等,再到应用在医疗、考古修复、航空航空等各个方面,几乎无所不能;3D打印技术现今应该呈现出,只有你想不到的,没有打印不出来的......
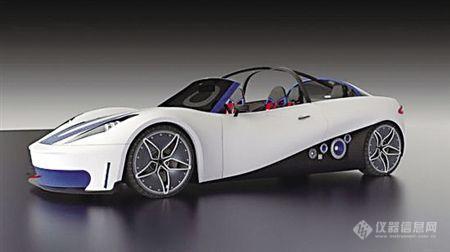
3D技术的优势:设计空间无限、改善产品设计、多样化生产不会增加成本、产品无需组装、缩短交付时间、制造技能门槛降低、不占空间,便携制造、节省原材料、材料无限组合、精确的实体复制等。3D技术的现状:目前还存在技术相对单一、设备便携性差、效率低下、材料受限制、精度不够,成本较高等问题。而制作出来的东西相对于工业化大规模生产出的产品毛刺较多,需要打磨,质量较差,难被消费者认可。但是随着我们科研人员的不断努力,相信这些技术问题都只是暂时的。而3D打印出来的产品也会最终打动消费者,获得市场的肯定。
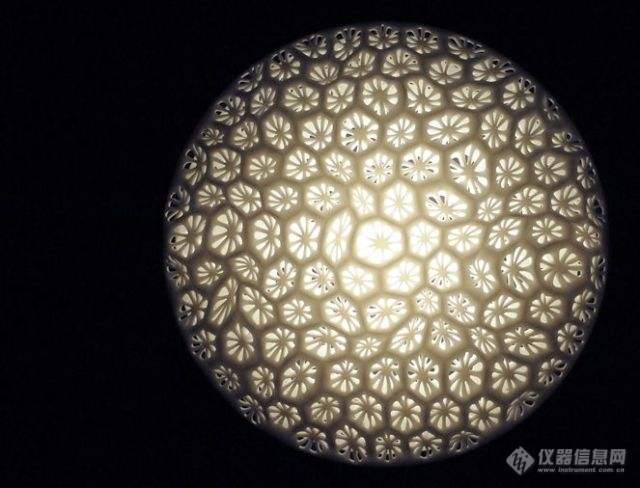
目前市场上主流的3D打印技术包括:
FDM熔融沉积成型、SLA光固化快速成型、DLP数码影像投射、SLS选择性激光烧结、DMLS直接金属激光烧结、PolyJet 紫外光固化喷射的液体感光树脂、MJP多喷嘴喷墨高分辨率逐层堆叠3D等技术。
今天来了解下3D打印技术中SLS工艺(选择性激光烧结),分析两批钴铬镍铁合金(也被称为微熔体CCM-MC)。在航空工业中,这种合金经常用作涡轮叶片,当然也会有其它的应用。通常,使用液体金属物化法得到这些粉体,即采用高速气流或者喷射的水使熔融的金属破碎成液滴,然后在水幕或油幕中迅速冷却得到粉体。研究的两批微熔体CCM-MC样品的化学组成和颗粒形状都是相同的,但是粉体样品的外观检查却发现两者的凝聚性略有差异。因此,两种粉体被分为粘性的(粉体样品A)和非粘性的(粉体样品B)。对两种粉体样品的磁距进行测试,发现两者均为顺磁性。
对两种粉体进行了初步的粒径分布分析。这不是必须要做的测试,但是与粒径相比,粒径分布的微小变化对其应用有更大的影响。相比于其他测试方法,粉体流动更加敏感,因此,可以更好的表现出这种影响
使用静态光散射的干法分散样品池对粒径分布进行分析。下图描述了测试的结果。结果显示主要的区别似乎是粘附性更强的样品中多了极少量的细颗粒。尽管如此,粒径和粉体流动直接的关系不是如此简单。在达到临界值时,细颗粒的添加确实会影响内聚力,但是影响效果取决于很多因素,包括化学组成、静电作用和湿度。为了得到流动行为的准确的图谱,仅仅分析粒径是不够的。
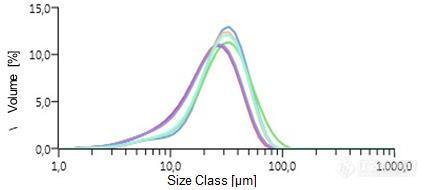
图1:两种粉体的静态光散射重复测试图谱,粉体A的测试图谱是红色和紫色曲线,粉体B的测试图谱是另外的一些曲线,这些曲线更符合正态分布。可以看到,横坐标为对数坐标,两种粉体在粒径分布上是非常相似的。
两种测试方法• 粉体单元的测量
• 通过简单的剪切测试来评价剪切质量
两种测试均采用安东帕公司的MCR 302流变仪,实际上,任何一款MCR xx2和MCR xx1流变仪均可以完成粉体流体的测试。
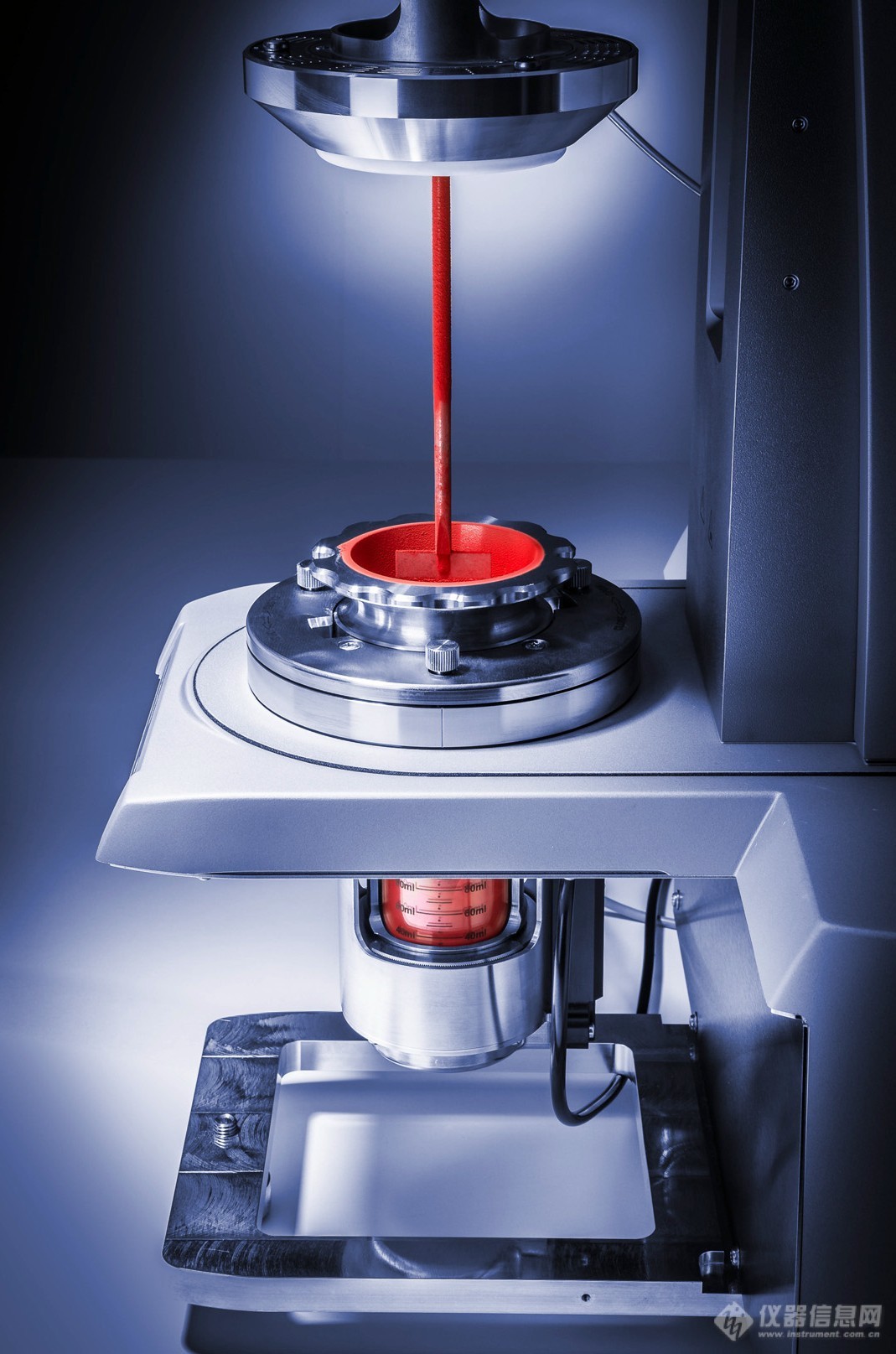
安装了粉体单元的MCR 302 WESP流变仪,粉体单元的密封池中填充了红色的涂料粉体
粉体单元的测量:
测试所使用的粉体样品的量大约是90克(大致与粉体单元所要求的最小体积100ml相对应)。对于每次测试来说,粉体样品的量必须保持不变,否则很难保证重复性。
采用粉体样品的流化曲线(见图4)去分析样品制备的可重复性。这表明了要实现完全的重现性需要多少气体流量。也可以简单的目测,但是使用流化曲线更精确。
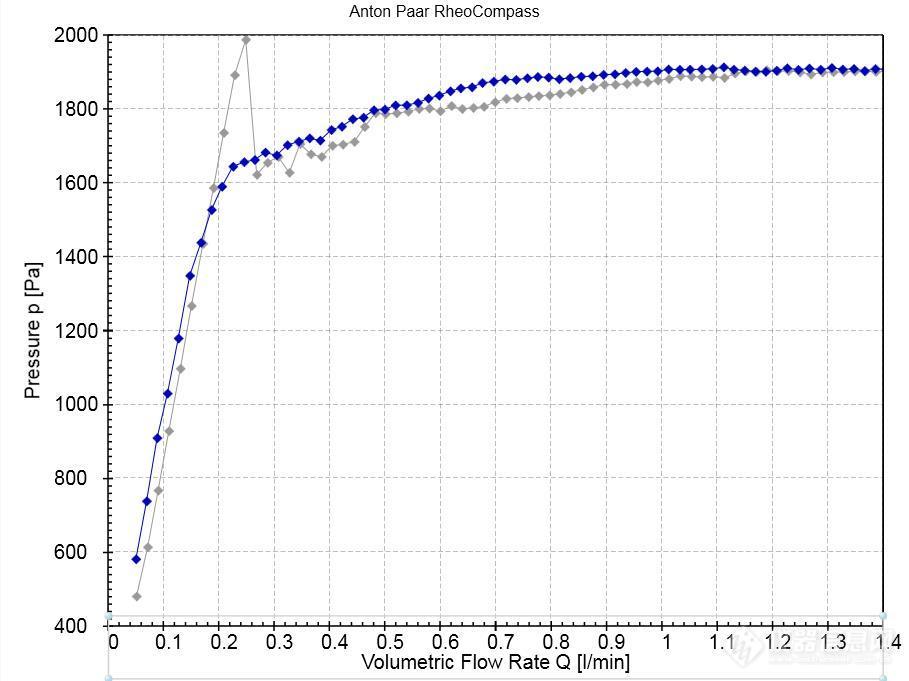
图2:无粘结性的粉体样品B的压力和气体体积流量的关系图。灰色曲线:增加体积流量;蓝色曲线:降低体积流量
灰色曲线的峰值显示了起始流发生在0.3L/min的位置,在1.2L/min,曲线走平,说明样品流化完全。因此在样品制备过程中,使用1.3L/min的体积流量,通气1min。
使用质量控制应用中的标准模板,即流化步骤之后就是测试步骤。.
尽管两种粉体样品的粒径分布非常相似(图1),但是他们测量得到的扭矩却有明显的差异(图3)。使用20个测量点的平均值来计算内聚强度(见表1 )。
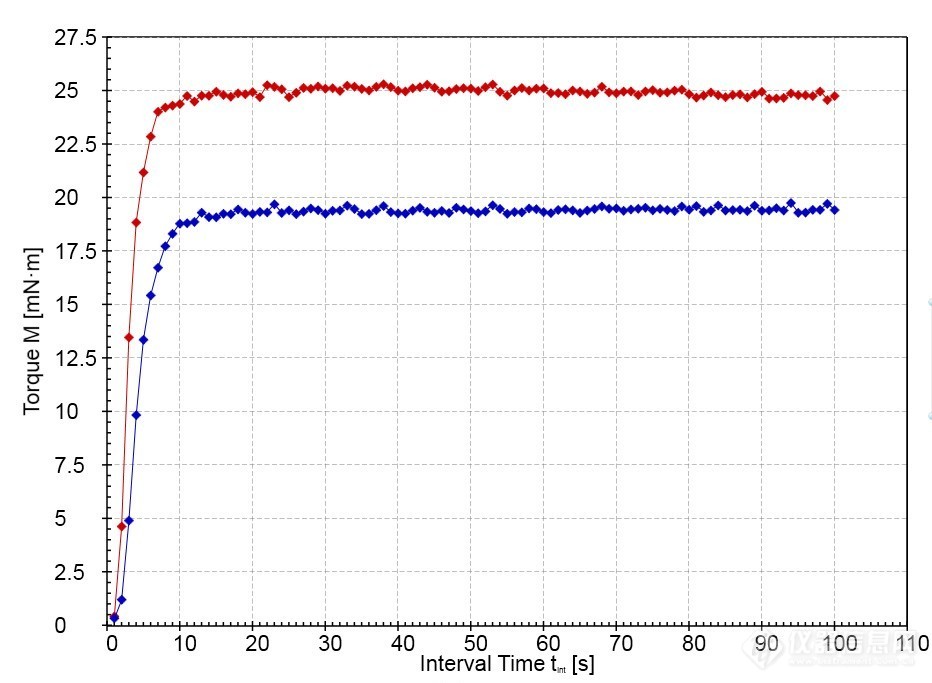
图 3:扭矩曲线:红色曲线对应着粉体样品A的黏着力,蓝色曲线对应着粉体样品B 的黏着力
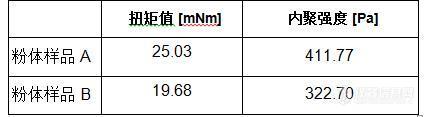
表 1:使用粉体单元测量得到内聚强度
为了证明这个方法的可重复性,对粉体样品B进行了7次样品填充和测试(见图4)。粉体样品A也得到了同样高的可重复性。
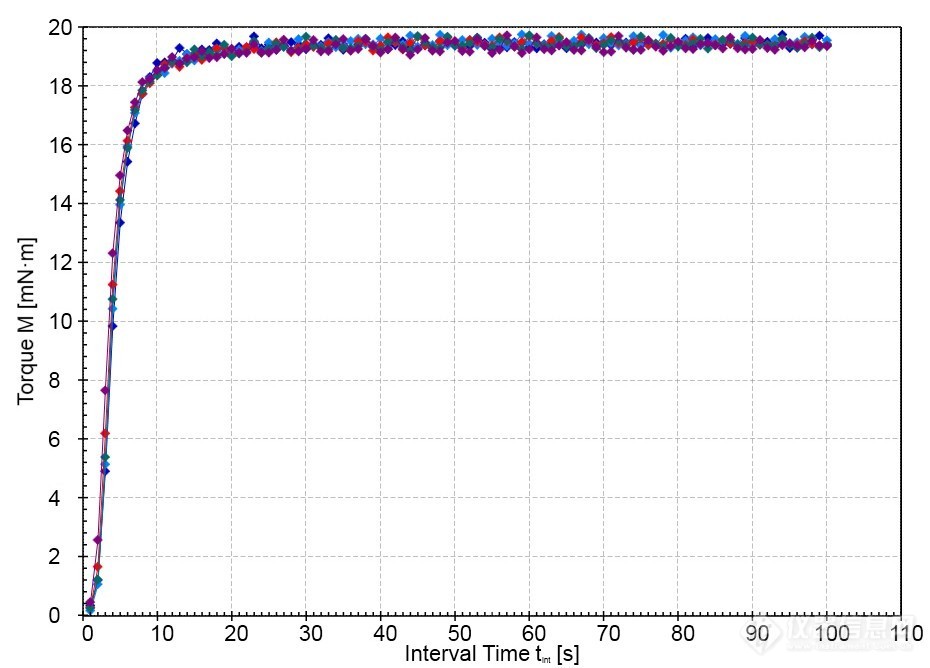
图 4:粉体样品B连续7次测试结果的图谱,计算得到的内聚强度(和相关扭矩)的偏差小于0.5%
剪切模拟测试:
使用量筒或者类似的有刻度的容器称量粉体样品(25ml或与其相等的堆积密度)。或者,也可以用重量法来称量粉体样品。.
为了更容易的得到一个合适的剪切面,粉体样品必须转移到盘子上得到一个锥形的堆。通过使用简易的漏斗可以实现(图.5a)。
必须小心移动漏斗来避免破坏锥形。对于没有粘着性的粉体样品来说尤为重要。.
MCR的线性马达将Krebs转子降至粉体锥顶。然后,缓慢的转动转子。需要注意的是,在剪切过程中,粉体必须一直和转子相接触。转子边下降边旋转以得到一个平坦的剪切面(图.5b)。测试步骤模拟了20μm剪切的SLS工艺(图.5c)。
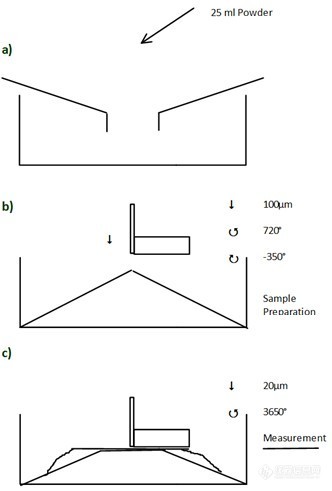
图5 :剪切过程示意图
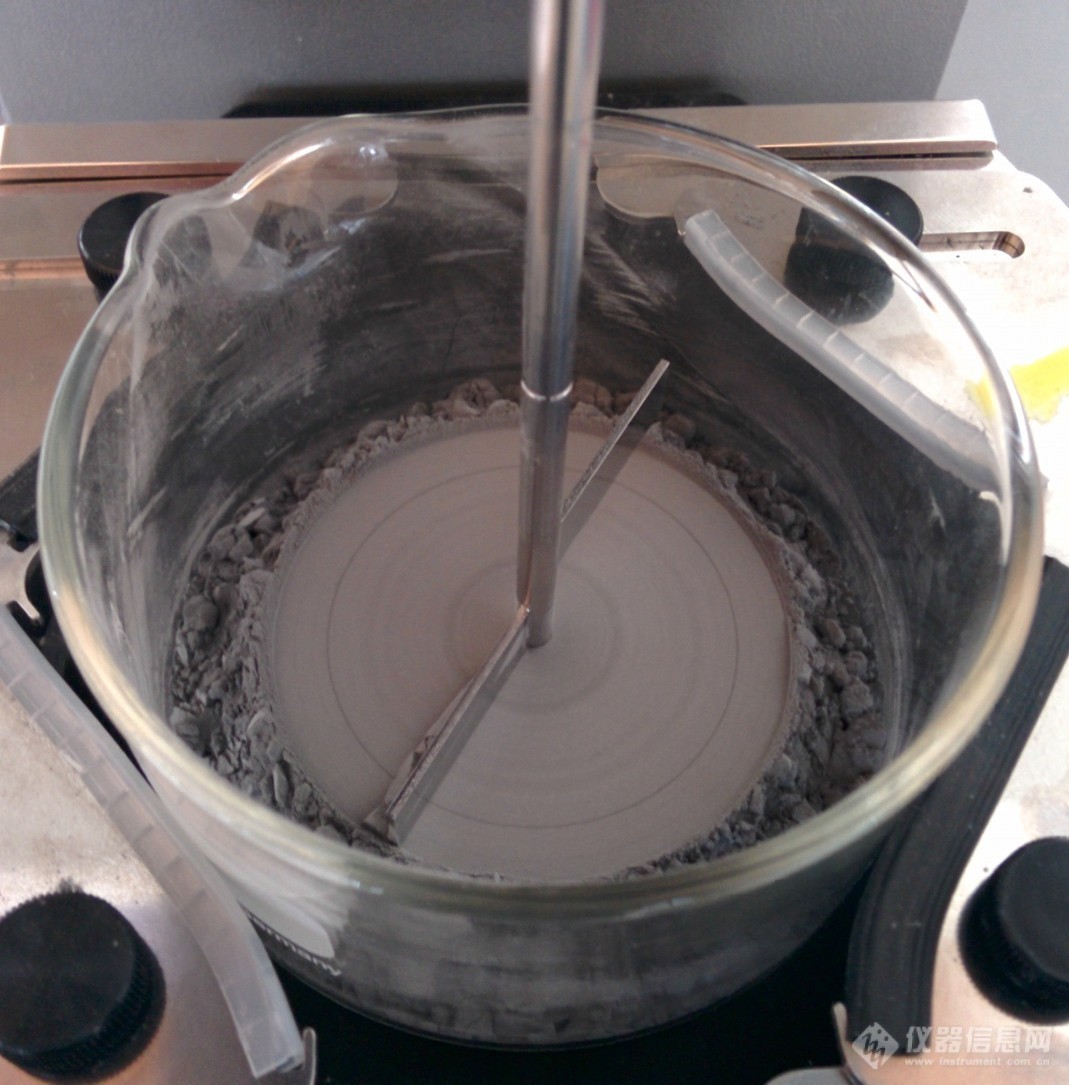
图6:粉体样品A的剪切实验结果。样品的剪切质量不高(剪切面上的圆形线)
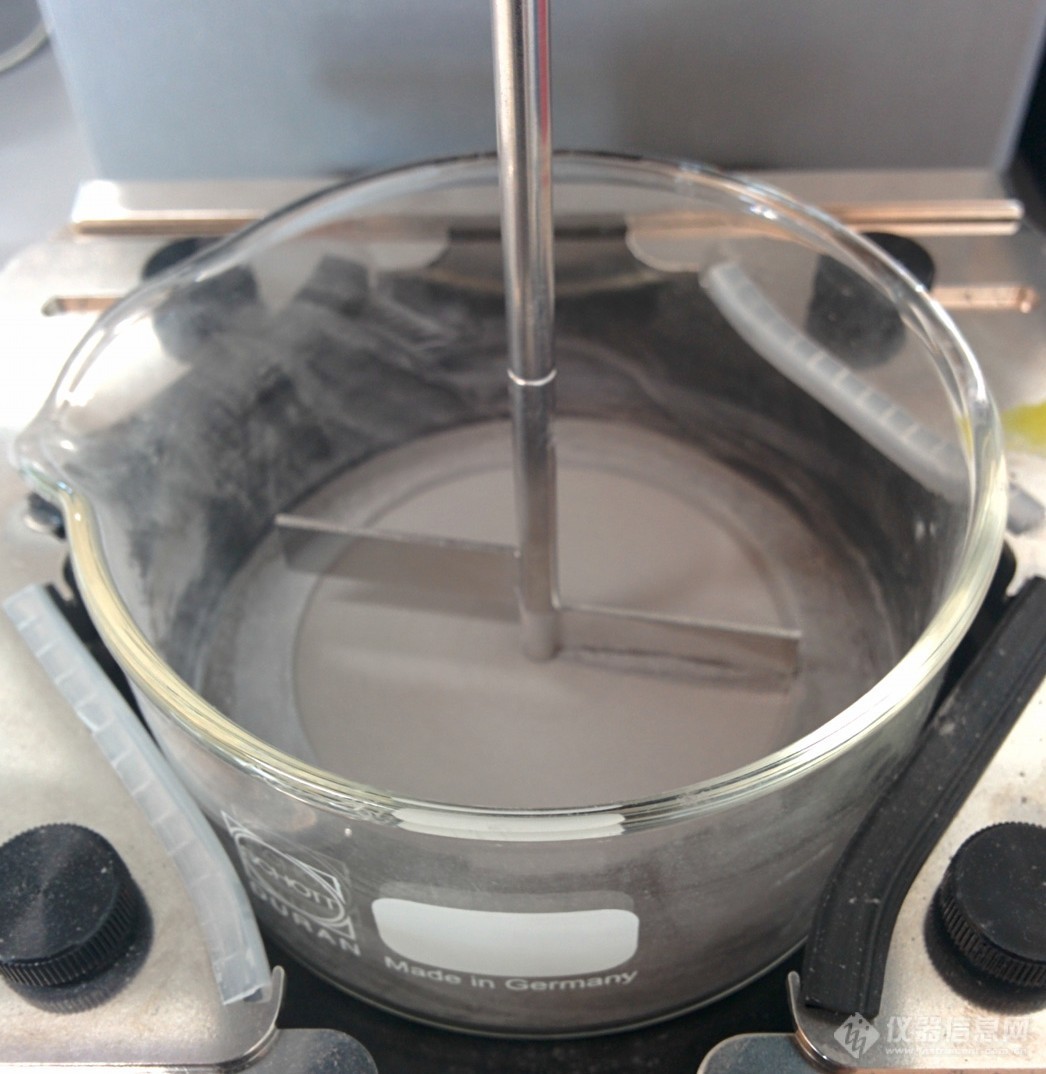
图7:在剪切测试中,和粉体样品A相比,粉体样品B的表面结构更加平滑
总结从上述测试展示了区分相似粉体样品的方法,分别是目测法和易于使用的QC应用(包含报告功能)。
这两种方法都可以清楚地区别粉体样品,同时可以看到,采用SLS工艺的粉体样品B明显更好。
粉体单元是一个可以得到高重复性的粉体流动性质(如内聚强度)数据的全自动设备。剪切方法是模拟SLS工艺的一个简单的实验,可以对剪切面进行简单的目测。在剪切过程中监测扭矩可以得到更多的信息。
逻辑上说,下一步可以对SLS工艺得到的粉体样品在使用过程中发生降解进行可行性研究。
更多精彩内容,请关注:https://www.anton-paar.cn/products/group/rheometer/?utm_source=gongkong&utm_medium=online-ad&utm_campaign=cn_C-00039998_online-portal

提交
产品简介 | ALAB 5000 饮料工业自动化实验室
活动回顾 | 江南大学生物制造“产教融合、协同创新”论坛
台式全自动流变仪
饮料工业自动化实验室
食品工业中的在线 NaCl 盐水浓度测量